Plastic crates are a ubiquitous product used across various industries, from logistics to agriculture. The manufacturing process of plastic crates involves several precise steps, each crucial in ensuring the final product meets the required standards for durability, performance, and cost-efficiency. In addition, plastic crates come in a variety of types and offer customizable options that cater to specific business needs. This article will walk you through the process of plastic crate manufacturing, detailing each stage from design to production.
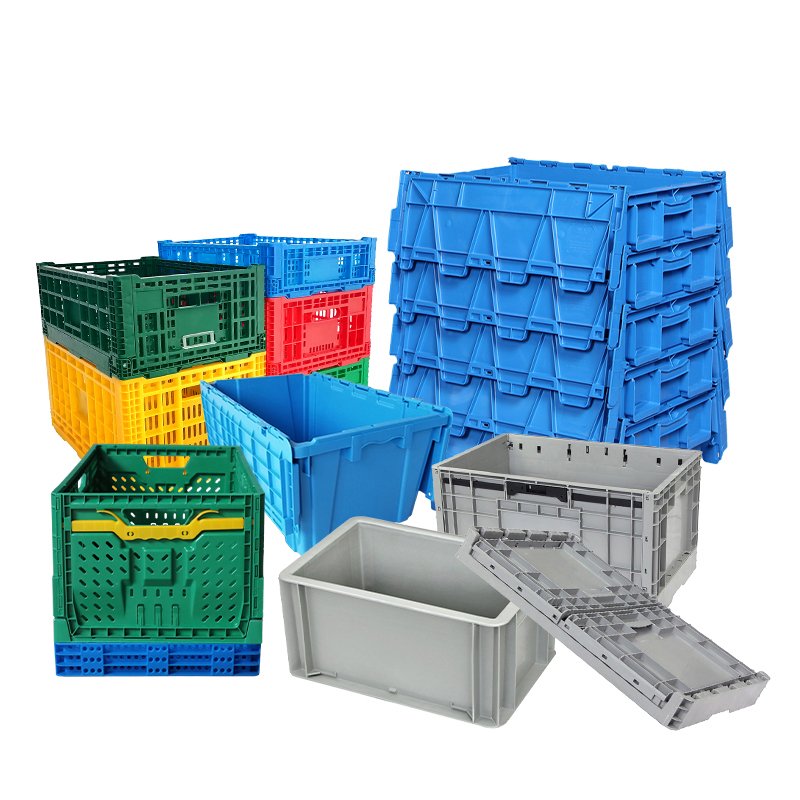
1. Product Design and Mold Creation
The first step in the manufacturing process is the design phase. At this stage, product engineers work closely with clients to define the dimensions, shape, and features of the plastic crate. The crate must be designed to meet the specific needs of the industry in which it will be used, such as stackability, load-bearing capacity, ventilation, and ease of handling.
There are several types of plastic crates that can be designed to suit different applications:
- Nesting crates: These are designed to fit inside each other when not in use, saving space during storage.
- Ventilated mesh wall crates: These crates are designed with mesh walls to ensure airflow, ideal for storing perishable goods like fruits or vegetables.
- Solid wall crates: These crates have solid walls and are often used for products that need more security or protection from external elements.
- Foldable crates: These are designed to be collapsible, which is useful for saving space when the crates are not being used.
Once the design is finalized, the next step is mold creation. Molds are critical for forming the shape of the crate. The mold-making process is precision-driven and often involves high-quality steel or aluminum, designed to withstand multiple uses. The cost and time involved in mold creation can vary depending on the complexity of the design, but they are crucial in producing consistent, high-quality crates.
2. Material Selection
Plastic crates are typically made from high-density polyethylene (HDPE) or polypropylene (PP), both of which offer durability, resistance to chemicals, and the ability to withstand extreme temperatures. The choice of material depends on the intended use of the crate. For instance, HDPE is often used for crates that need to withstand UV rays or chemicals, while PP might be chosen for lightweight crates that still require substantial strength.
The material is sourced in the form of pellets, which are then processed in the next stage.
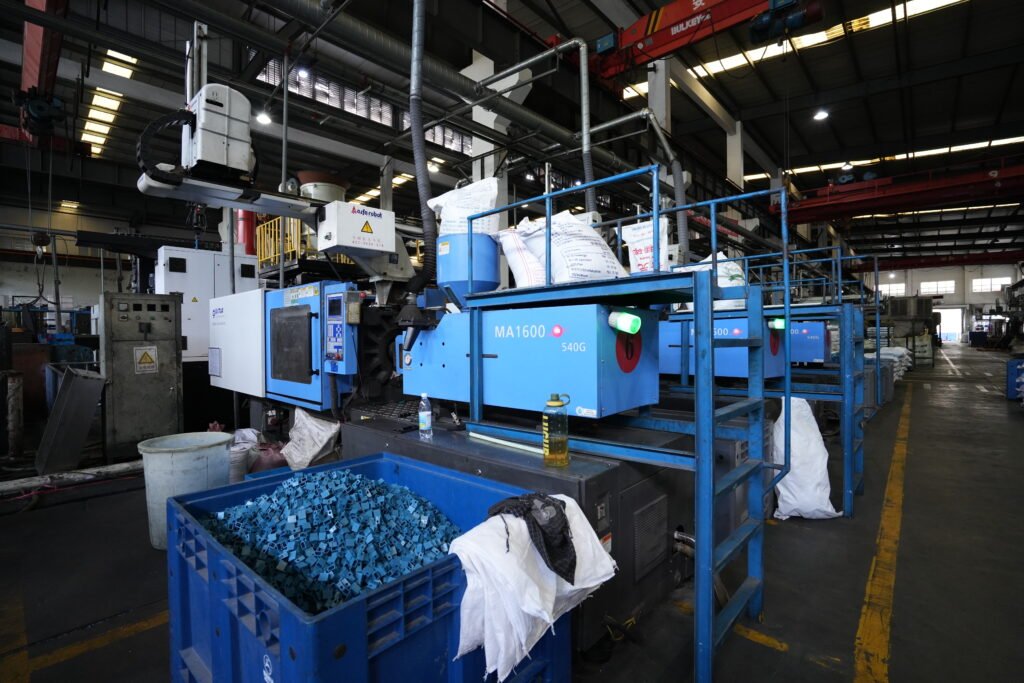
3. Injection Molding Process
Once the mold and material are ready, the next step in the manufacturing process is injection molding. In this process, the plastic pellets are fed into a hopper and then heated in an extruder. The molten plastic is injected into the mold under high pressure, ensuring that the plastic fills every corner of the mold. The mold is then cooled, and the crate solidifies into its final shape.
Injection molding is a highly efficient process that allows manufacturers to produce crates in large quantities. It also ensures that the crates are uniform in size and strength, meeting the required specifications. This process is ideal for producing crates with intricate details or specific structural features.
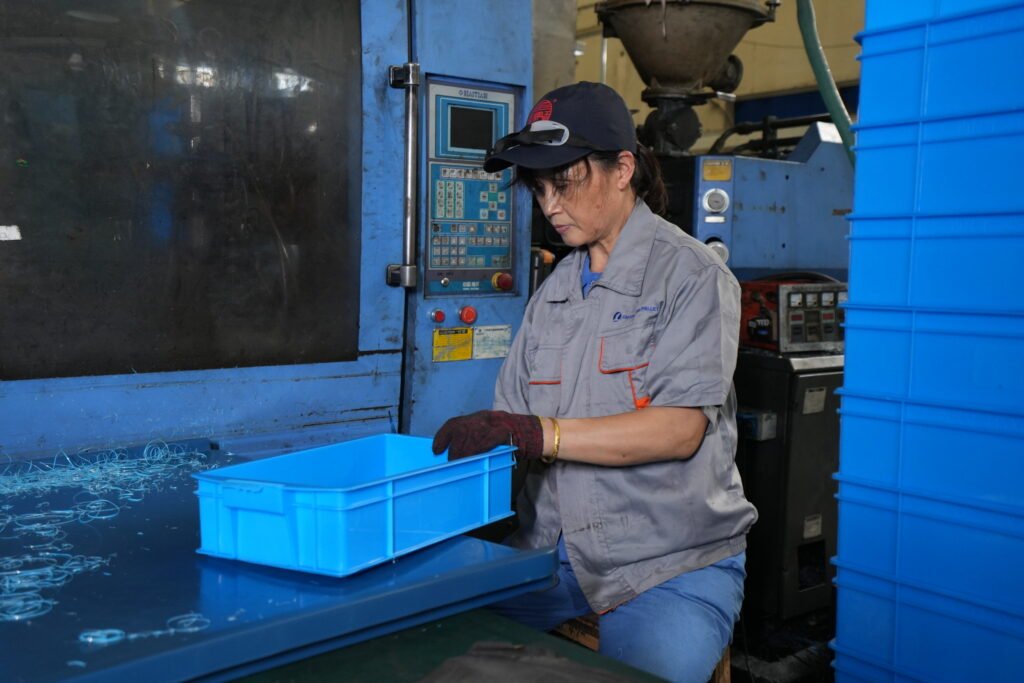
4. Customizable Options for Plastic Crates
Plastic crates can also be customized to meet the specific needs of clients. Common customization options include:
- RFID tags: For businesses that require efficient tracking of inventory, RFID tags can be embedded in the crates. This enables easy tracking throughout the supply chain, ensuring that products are moved and stored efficiently.
- Custom silk-screen printing: Companies often want their logo or branding on their plastic crates. Silk-screen printing is used to add logos or designs to the surface of the crate, offering a cost-effective way to personalize crates for different business purposes.
These customization options not only enhance the functionality of the plastic crates but also improve brand visibility and streamline operational processes.
5. Cooling and Ejection
After the mold is filled, the plastic must be cooled. Cooling is done by circulating cold water through the mold or air-cooling it. The crate is left to cool for a few minutes to solidify fully. Once cooled, the mold is opened, and the newly formed plastic crate is ejected from the mold.
This step is crucial because improper cooling can lead to warping or uneven thickness, compromising the quality of the final product.
6. Quality Control and Inspection
After the crates are ejected from the mold, they undergo thorough quality control checks. This includes inspecting the crates for defects such as cracks, color inconsistencies, or dimensional errors. Some manufacturers also perform drop tests, load-bearing tests, and resistance tests to ensure that the crates meet industry standards for durability and functionality.
Any defects found are corrected before the crates move on to the next stage of production. This ensures that only high-quality products reach customers.
7. Packaging and Shipping
Once the crates pass the quality inspection, they are packaged and prepared for shipping. Depending on the customer’s needs, crates may be packaged individually or in bulk. They are then sent to warehouses or directly to customers, ready for use in various industries.
Conclusion
The process of manufacturing plastic crates involves a well-coordinated blend of design, material selection, molding, and quality control to produce a product that meets the diverse needs of industries around the world. Whether the crates are nesting, ventilated, solid-walled, or foldable, manufacturers can tailor the design to suit specific needs. Additionally, customizable options like RFID tracking and logo printing further enhance the functionality and branding opportunities for businesses. With the right manufacturing process and attention to detail, plastic crates are durable, cost-effective, and versatile products that serve a wide range of commercial and industrial purposes.